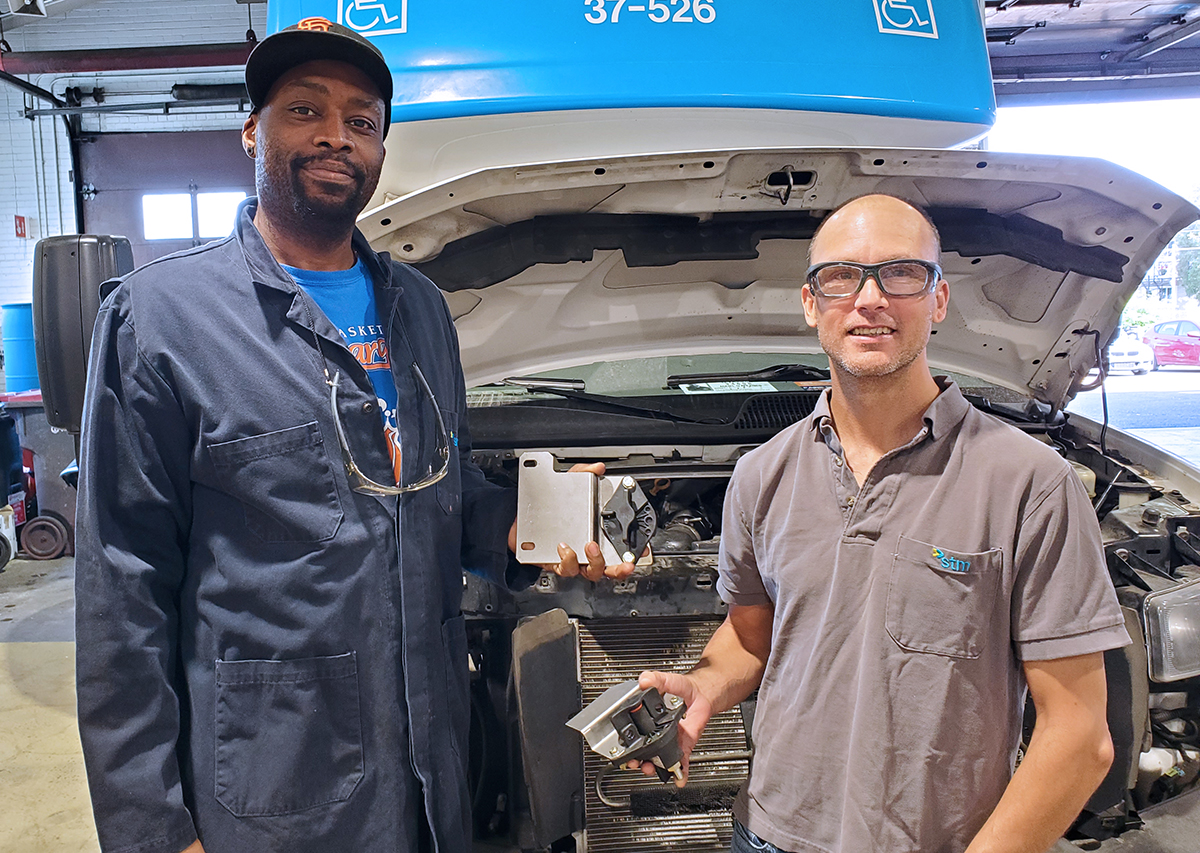
Fredzer Flamand, mécanicien de véhicules lourds routiers – Manufacturier, et Sylvain Provost, technicien – soutien technique à l’Ingénierie.
Le 27 mars dernier marquait l’implantation du premier dispositif de cadenassage élaboré par le Transport adapté (TA). Voyez comment ils ont procédé à la conception de cet outil.
La sécurité avant tout
L’équipe du transport adapté (TA) a mis en place un plan d’action au début de l’année 2023 visant l’implantation du cadenassage, tel qu’identifié dans le programme maitre. Celui-ci a pour but d’éliminer ou de réduire au minimum le risque d’exposition aux énergies dangereuses. Il permet de procéder à une tâche sur un équipement dont l’alimentation ou le démarrage inattendu ou encore le dégagement intempestif d’énergie accumulée pourrait survenir et provoquer des blessures.
Enjeux importants
Les véhicules du TA, qui emmagasinent 12 volts, doivent être cadenassés avant de procéder à leur entretien. Malheureusement, les dispositifs de cadenassage n’étaient pas adaptés pour les minibus. En effet, ceux qui roulent au diesel et à l’essence ne possédaient pas de système de cadenassage intrinsèque adéquat. La méthode en place endommageait les câbles d’alimentations des batteries du véhicule, demandait beaucoup de temps aux employés et n’était pas à 100% sécuritaire. « La santé et la sécurité, c’est important pour nous », partage Roch Cyr, contremaitre à l’entretien du TA.
Un dispositif novateur
C’est ainsi que l’équipe du TA a effectué des recherches sur le marché, a adapté et intégré un nouveau coupe-batterie. Ce système rend beaucoup plus sécuritaire l’entretien des véhicules. Fixé de manière permanente à l’intérieur du capot, l’appareil permet d’éliminer l’énergie électrique du minibus. Ce processus protège non seulement les mécaniciens des démarrages intempestifs, mais évite aussi de perdre la charge de la batterie durant de longues périodes d’inutilisations.
« L’objectif est que le cadenassage soit plus facile. Le dispositif fonctionnera pour toute la durée de vie du véhicule. Cela sauve beaucoup d’argent et diminue la durée des travaux. Maintenant, on procède beaucoup plus rapidement. On ne défait plus la batterie comme avant : on installe l’appareil, on ferme l’interrupteur et on met le cadenas », nous dit Roch.
![]() |
![]() |
–
Le coupe-batterie intégré près de la batterie au centre du véhicule |
–
Le coupe-batterie intégré dans le capot du minibus |
– |
Repensé par des employés d’ici
L’adaptation du dispositif a été imaginée par l’Ingénierie bus de concert avec les mécaniciens du TA et les tôliers de l’usine Crémazie. La collaboration et le professionnalisme de messieurs Sylvain Provost, Technicien, Soutien technique, Intégration, Ingénierie bus, Samuel Côté, ingénieur principal, Génie manufacturier et Sopheak Seang, Travailleur de métal en feuilles à l’Usine Crémazie, ont permis une réalisation interne efficace. De plus, le projet n’aurait pas été possible sans le précieux travail de ces divers employés :
- Fredzer Flamand, Mécanicien de véhicules lourds routiers
- Marc-Antoine Morin-Maltais, Technicien, Soutien technique, Intégration, Ingénierie bus
- Roch Cyr, Contremaître au TA de jour
- Sébastien Boulianne, Chef de section, Génie manufacturier
- Willian Yuki Fatiga Onuki, Ingénieur, Intégration, Ingénierie bus
Un grand déploiement
La mise en place de l’appareil est échelonnée sur plusieurs mois. Au Transport adapté, il existe 102 véhicules. Pour le moment, les coupe-batteries sont fixés sur l’ensemble des minibus Ford. Des démarches sont en cours pour l’adaptation sur les minibus de modèle GM. Le projet fonctionne si bien, qu’il est présentement en implantation sur les divers véhicules de services de la STM notamment des véhicules de style pick-up et sur les remorqueuses.
Félicitations au Transport adapté et à tous ceux qui ont contribué à ce projet!
Partager